2019 NASA Student Launch Competition
Payload Mechanical Lead
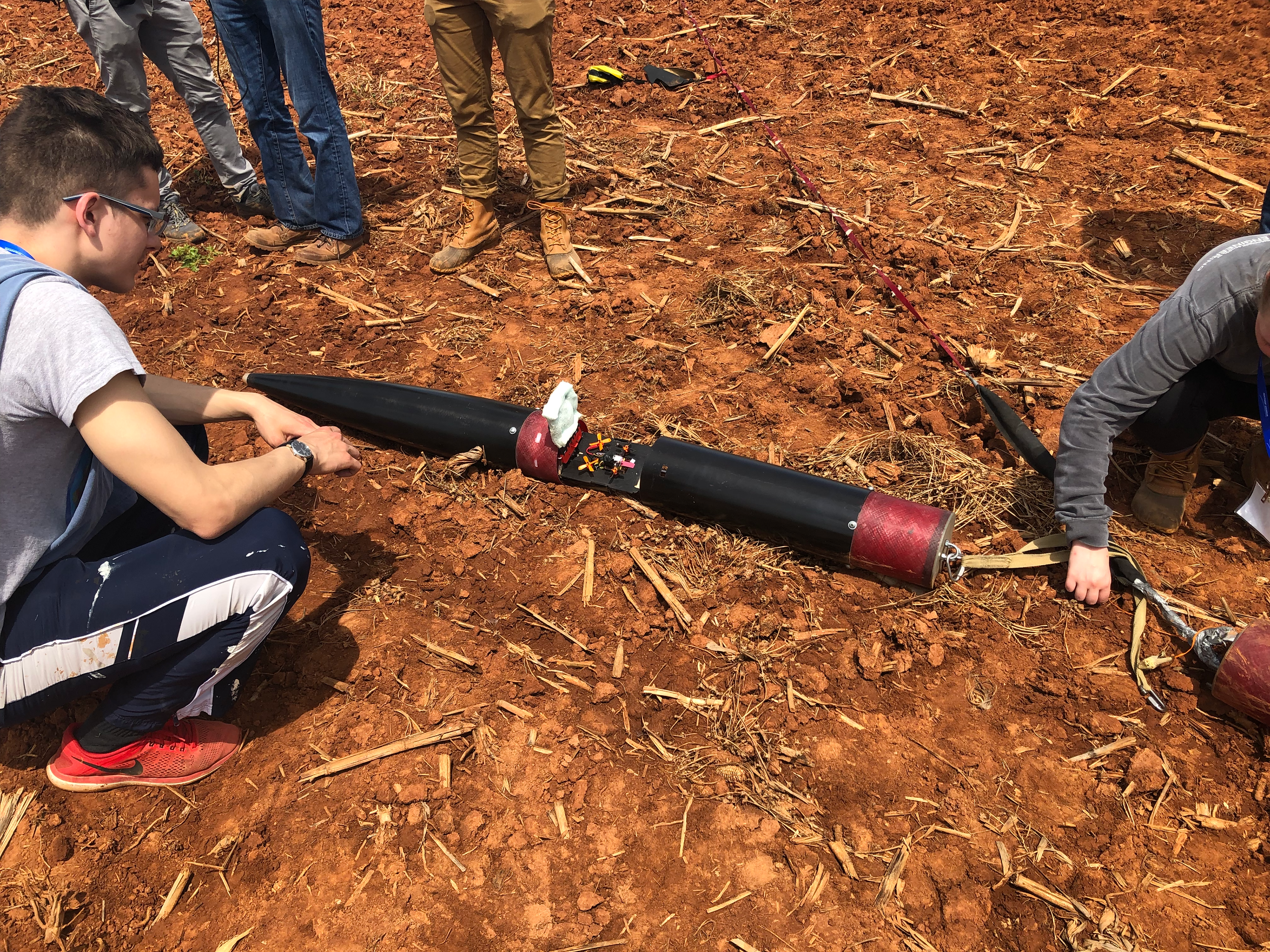
Payload Section after deployment.
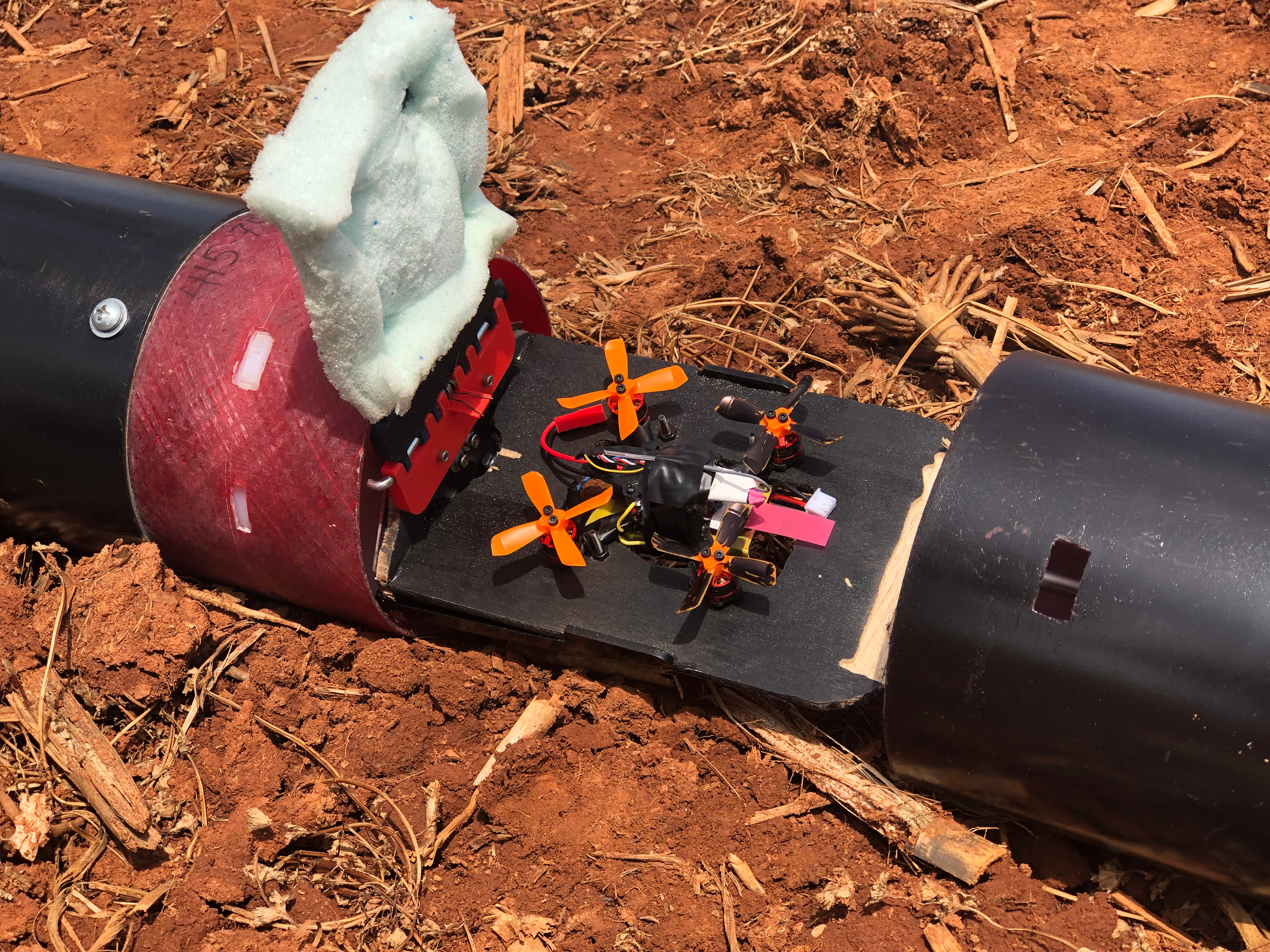
Close up of UAV after deployment.
Loading of Rocket onto Launch Rail. Me pictured in center.
Subteam picture, me center in white.
Launch of the rocket on competition day.
Competition Results: Flew 81 feet below our target altitude. UAV deployment system survived flight and worked well, pressure in cylinders was low from sitting on the pad for longer than planned. UAV batteries drained too much to take off but was unharmed and operable.
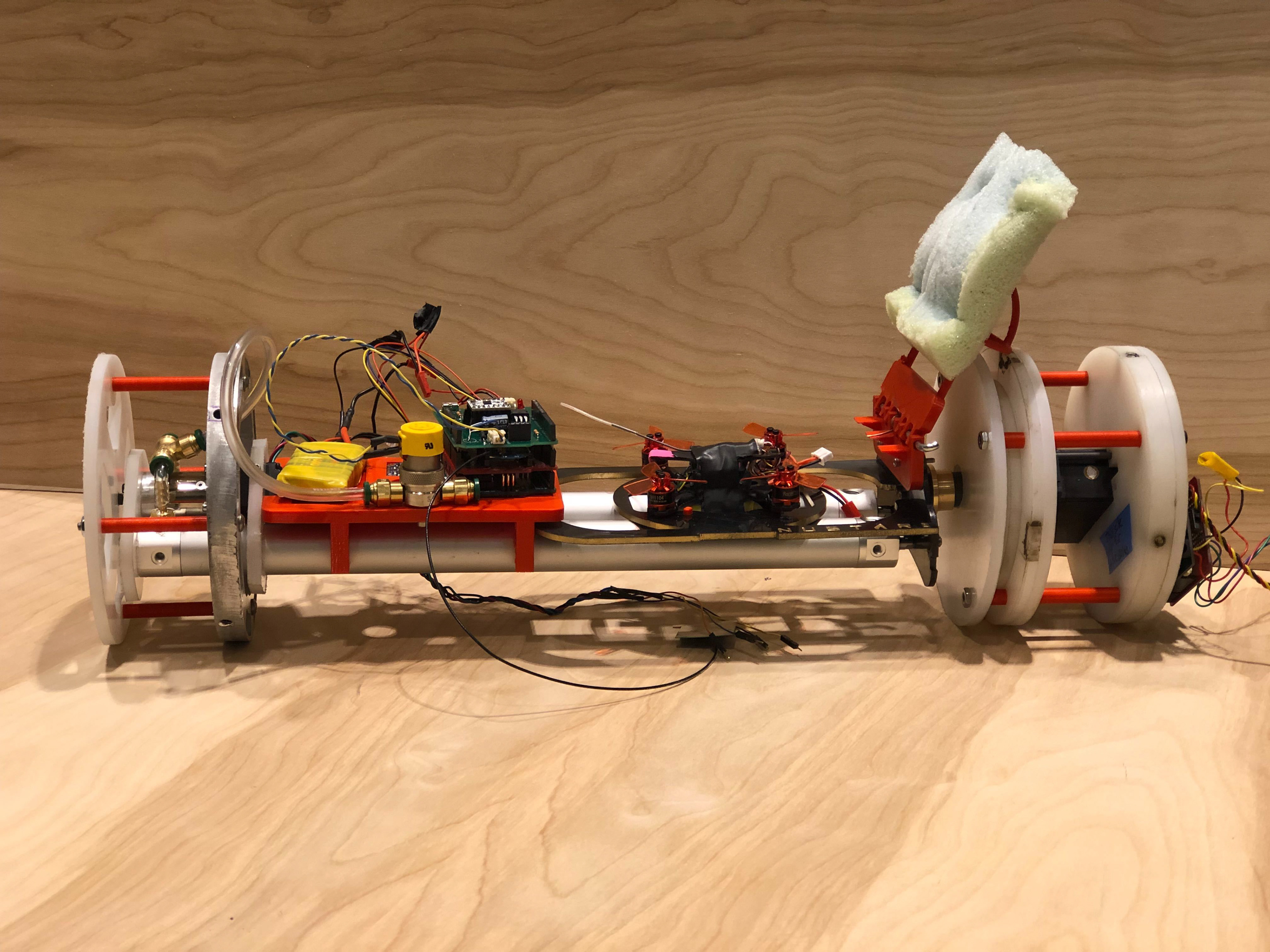
Completed Payload
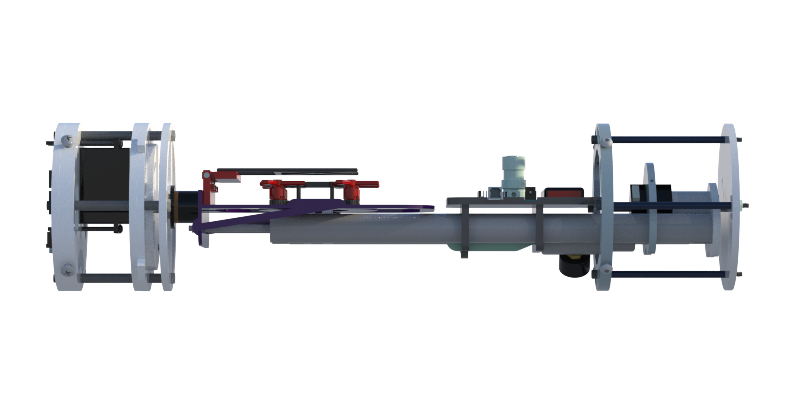
Render of Paylaod
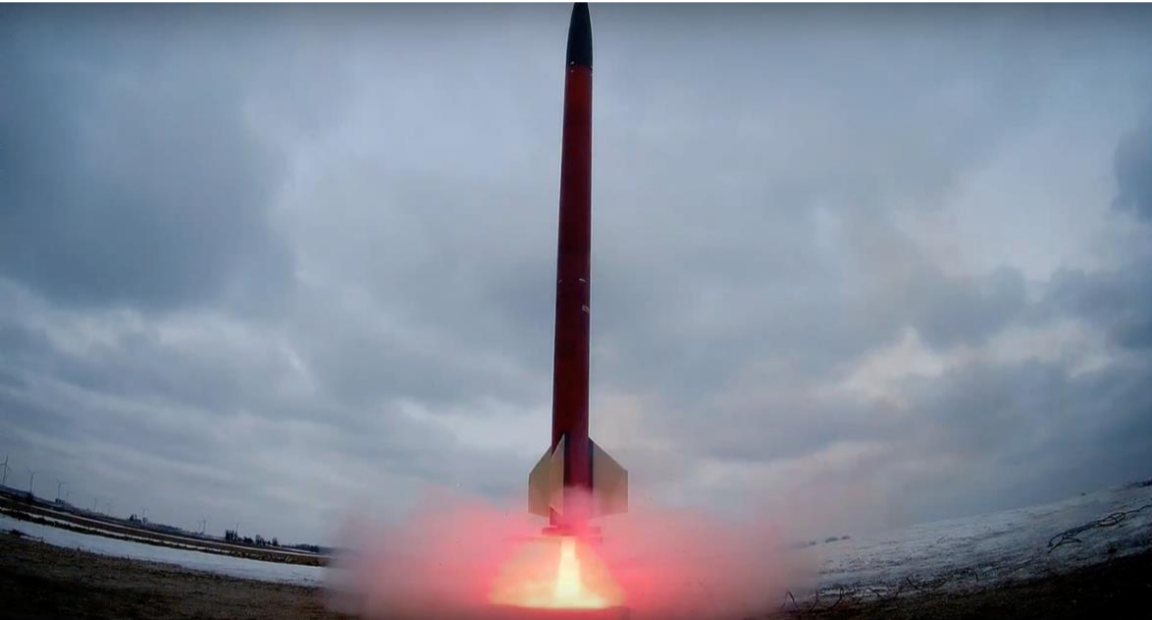
Feb 2019 Launch
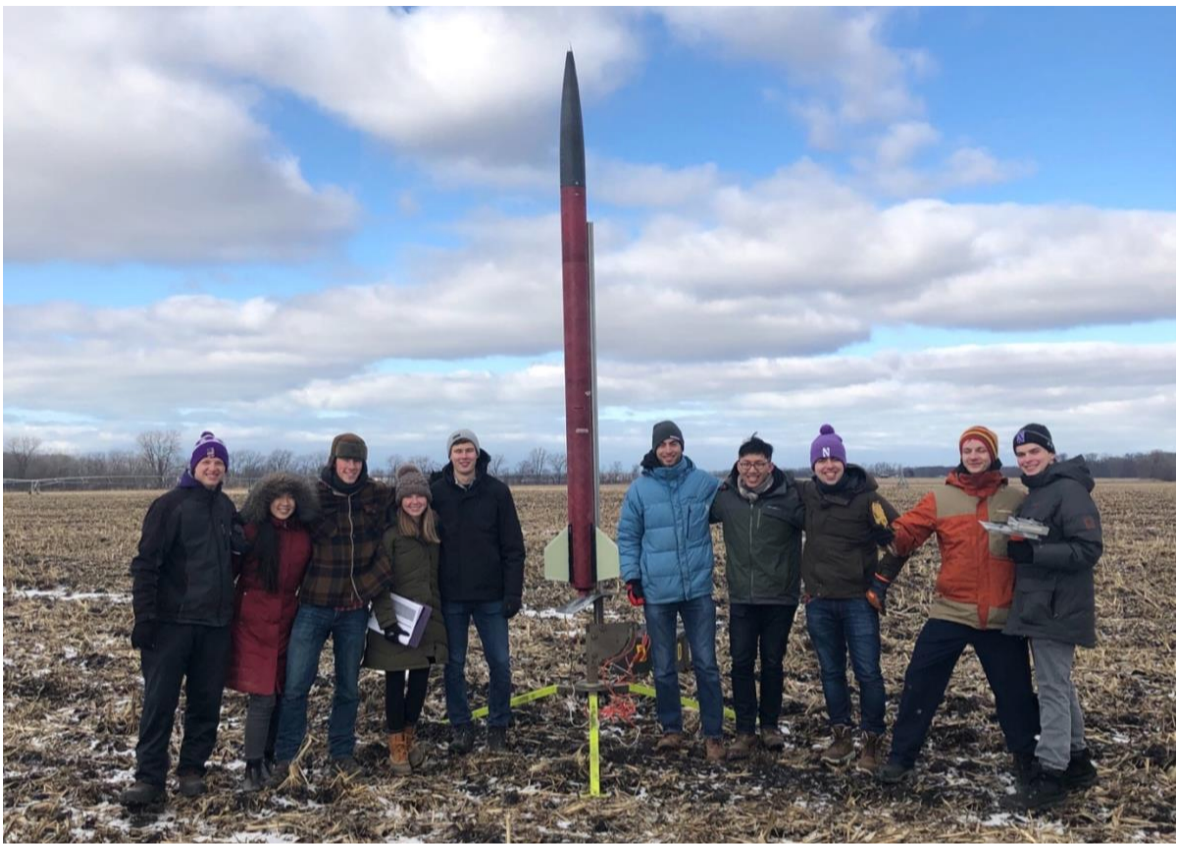
January Launch
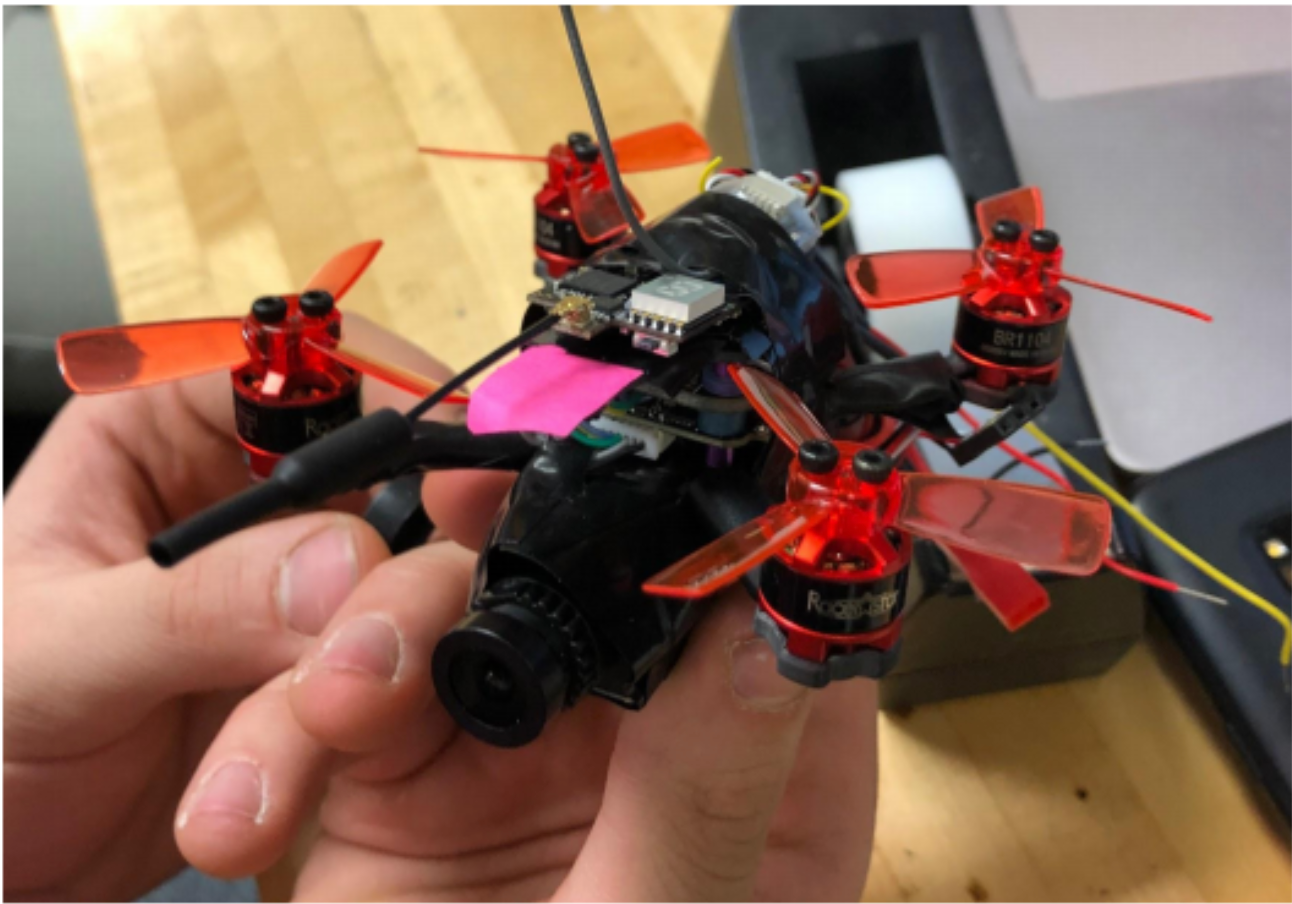
3in x 3in Custom Drone
Fly to 5400 feet, land safely and deploy remote controlled UAV (quadcopter) and deploy a beacon at a designated area.
Pictured above is the payload section of the rocket, containing the UAV and Deployment System
Features automatic orientation correction system. Pneumatic deployment system and micro drone. Simplified manufacturing using stacked water-jet plates and 3D printing. Easy subassembly construction allowing quick instillation in the rocket before flight. Modularity allows fo the replacement of parts and swapping of CO2 canisters with ease. Mass optimized bulkhead (Hyperworks) allowed for added strength and safety with minimal weight penalty.
2018 NASA Student Launch Competition
Payload Design and Manufacturing
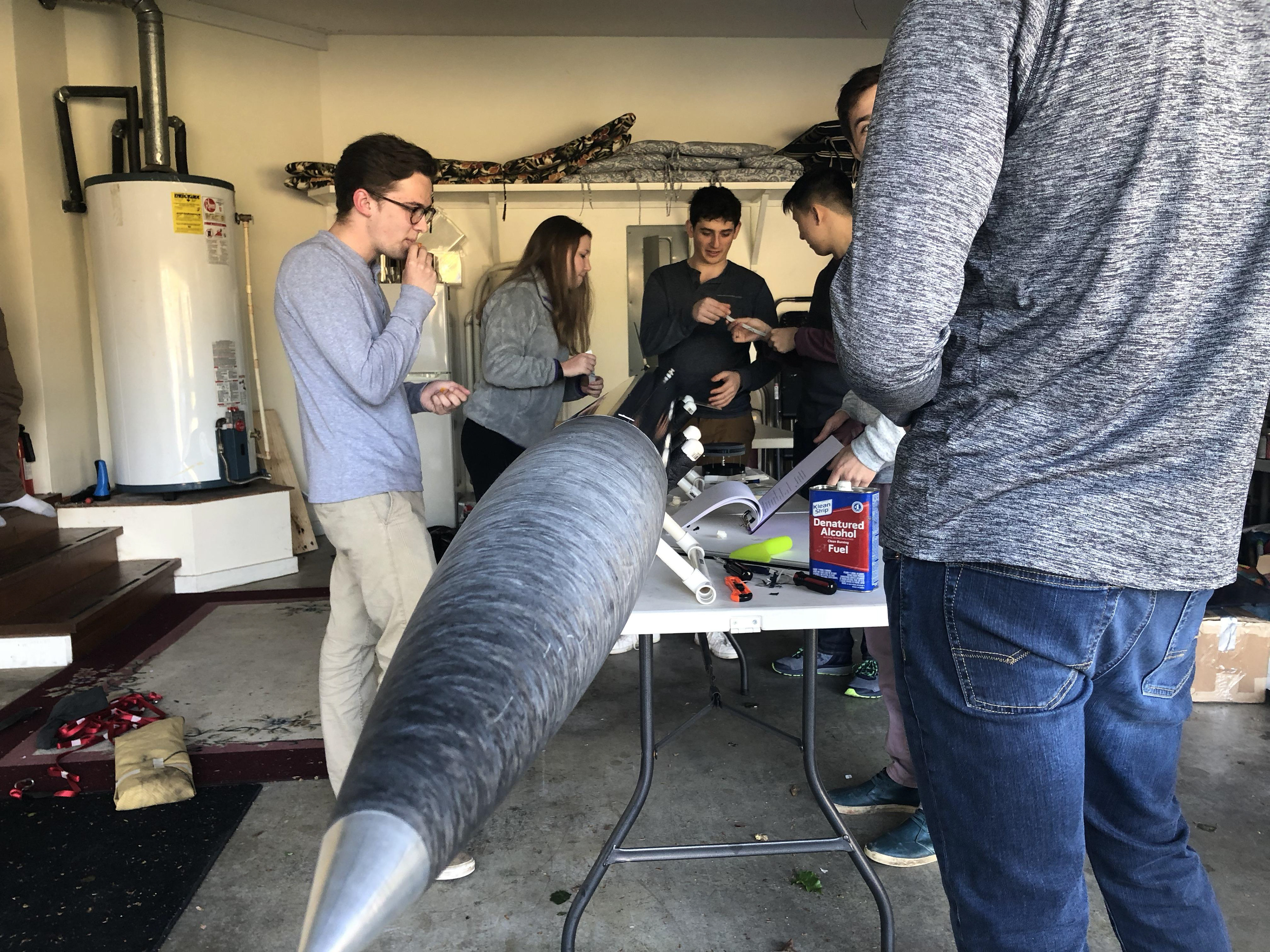
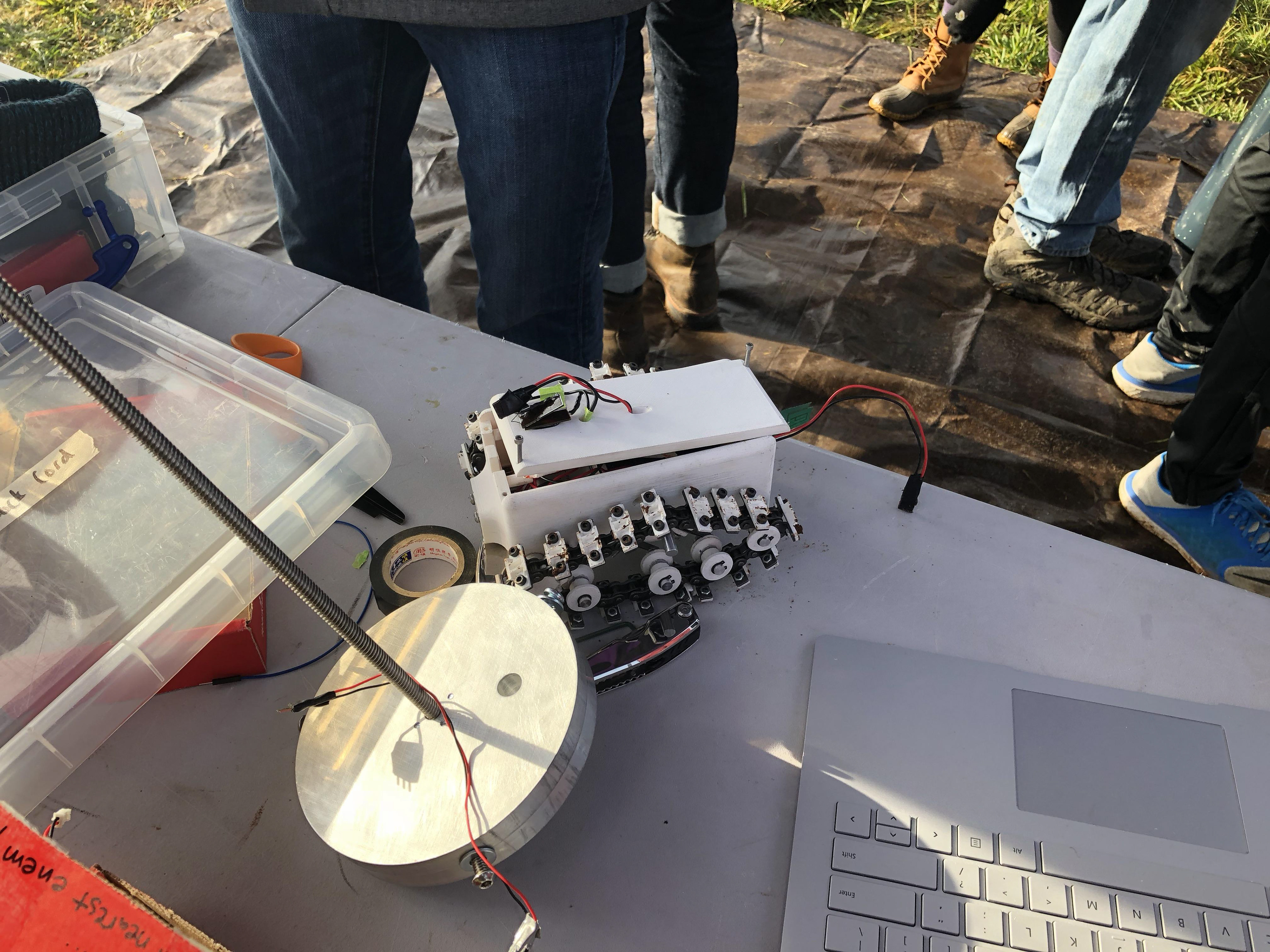
Competition: Fly to a mile autonomously deploy rover after landing.
Rover must exit rocket body and deploy solar cells at least five feet from landing site.
2017 NASA Student Launch Competition
Payload Design and Manufacturing
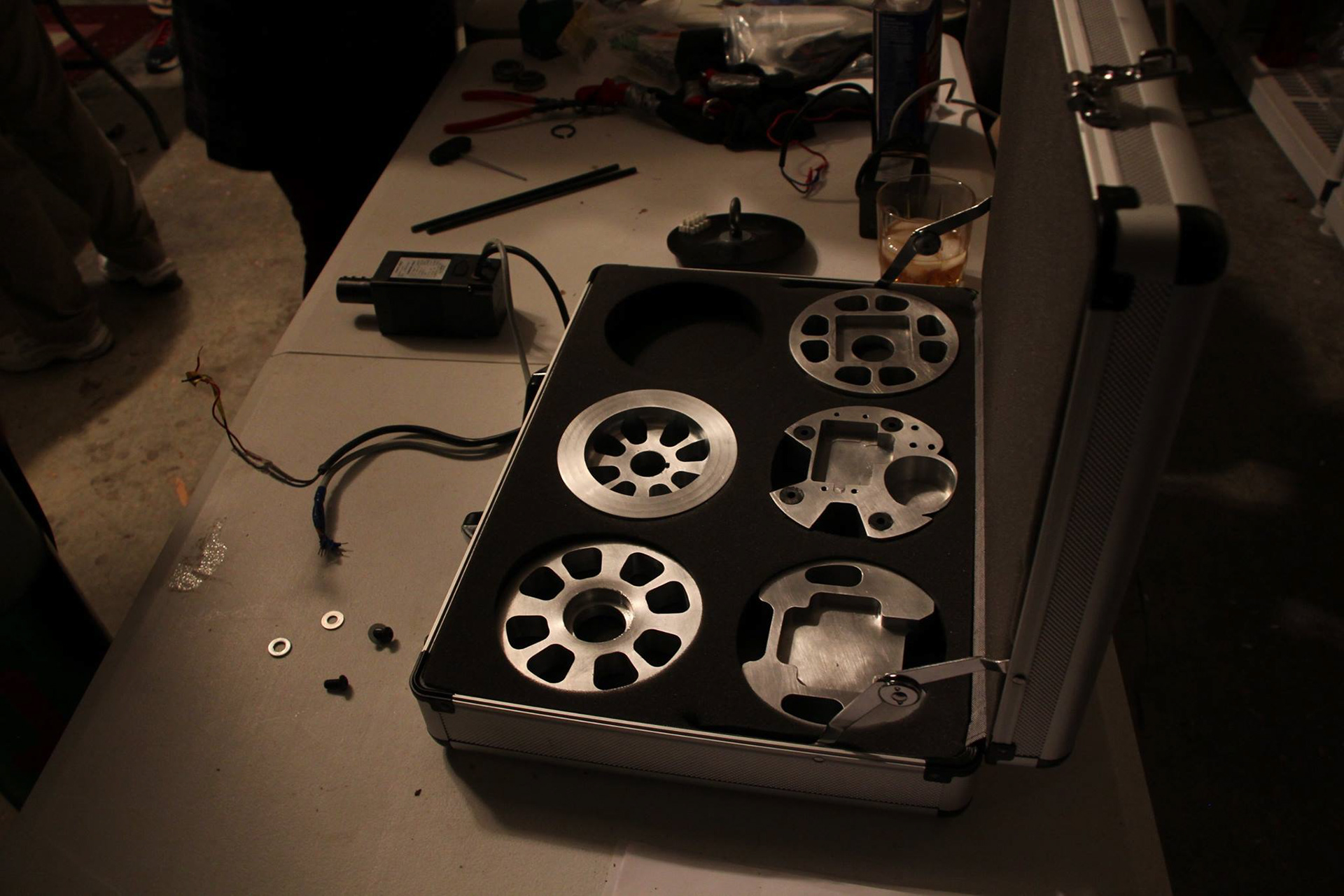
Competition: Fly to a mile, rotate 270 degrees mid air.
Was achieved with a aluminium flywheel inducing angular momentum on the rocket after motor burnout.
2016 Midwest Rocketry Competition
Payload Design
Competition: Fly to 4000 feet. Land safely, fly again to 3000 feet using same motor.
[Top Right] Failure during test launch
Altitude change was achieved by use of an Air-break [Top Left] deploying mid-flight: